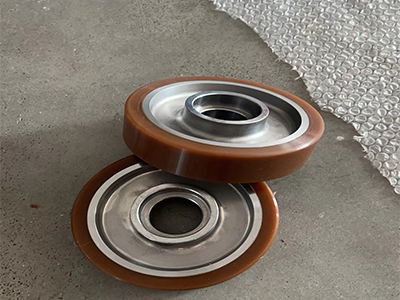
In the realm of conveyor belt maintenance, polyurethane belt cleaner scraper systems play a pivotal role in ensuring the efficiency and longevity of belt operations. These systems are categorized into primary, secondary, and tertiary belt cleaners, each serving a distinct purpose in the cleaning hierarchy.
Primary Belt Cleaners
Primary belt cleaners are the first line of defense against material carryback and spillage. They are strategically positioned at the tail pulley to remove the bulk of the residual material before it can accumulate. The durability and resistance of polyurethane to abrasion make it an ideal material for these cleaners, as they can withstand the rigors of continuous operation without significant wear.
Secondary Belt Cleaners
Secondary belt cleaners are designed to address the finer particles that may escape the primary cleaners. These are typically located just before the return idler and are crucial for preventing the ingress of fines into the belt's carcass, which can lead to premature belt failure. The polyurethane scrapers in this system are often finer and more flexible, allowing them to conform to the belt's surface and remove even the smallest particles.
Tertiary Belt Cleaners
Tertiary belt cleaners represent the final stage in the cleaning process. They are used to remove any remaining material that could affect the performance of belt or cause environmental issues. These cleaners often employ a more aggressive polyurethane scraper design, with a focus on high contact pressure and a robust construction to ensure thorough cleaning without damaging the belt.
In Conclusion
Polyurethane belt cleaner scraper systems are an essential component of conveyor belt maintenance. They operate in a tiered approach, with each level of cleaner addressing a specific aspect of material removal. The use of polyurethane ensures that these systems are both effective and durable, contributing to the overall reliability and efficiency of the conveyor system.