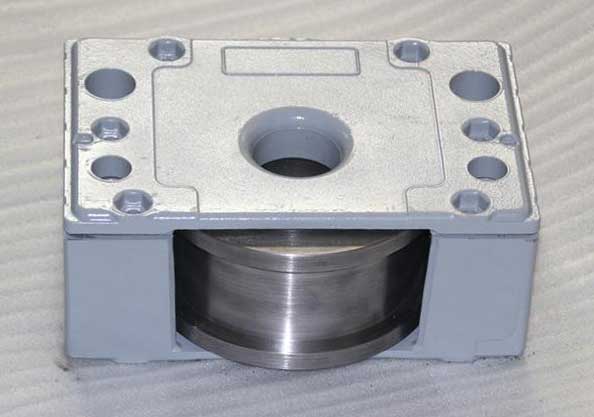
The vulcanization process of polyurethane forklift wheels is a specialized manufacturing technique that involves chemically bonding a polyurethane (PU) tread to a metal core. This process enhances the wheel’s durability, load-bearing capacity, and resistance to wear and tear. Vulcanized polyurethane forklift wheels are widely used in industrial applications due to their superior strength, adhesion, and longevity compared to mechanically bonded wheels.
Key Steps in the Vulcanization Process
1. Preparation of the Metal Core
The metal core (typically made of steel or aluminum) is first machined to the required dimensions.
Surface preparation is critical to ensure strong bonding:
Degreasing – Removing any oils, dirt, or contaminants using chemical solvents.
Sandblasting – Creating a rough surface texture to improve adhesion.
Priming – Applying a special bonding agent (adhesive primer) that chemically reacts with polyurethane during vulcanization.
700-950 kg high load capacity forklift wheel
2. Polyurethane Prepolymer Mixing and Preparation
Polyurethane is synthesized from polyols and isocyanates, which are mixed in precise proportions.
The prepolymer mixture may include additives such as:
Catalysts – To control the reaction speed.
Colorants – For product differentiation.
Reinforcements – To improve mechanical properties.
The polyurethane mixture is preheated to the optimal curing temperature.
3. Mold Preparation and Injection
The prepared metal core is placed inside a preheated mold.
The liquid polyurethane mixture is injected or poured into the mold, surrounding the metal core.
The vulcanization reaction begins as the polyurethane chemically bonds with the primed metal surface.
4. Vulcanization and Curing
The mold is maintained at a specific temperature and pressure to allow the polyurethane to cure properly.
During vulcanization, the polyurethane undergoes cross-linking, forming a strong and elastic bond with the metal.
The curing time varies depending on the polyurethane formulation and wheel size but typically lasts several minutes to hours.
5. Demolding and Post-Curing
Once the polyurethane is fully cured, the wheel is removed from the mold.
Some wheels undergo post-curing in an oven to further enhance mechanical strength and thermal stability.
The final product is cooled to room temperature before further processing.
6. Quality Inspection and Finishing
Each wheel undergoes a quality check to ensure proper adhesion and performance.
Deflashing and trimming are performed to remove excess polyurethane.
The final wheel may be machined or ground for precision finishing.
Different sizes of high load capacity forklift wheels
Benefits of Vulcanized Polyurethane Forklift Wheels
Feature | Benefit |
Stronger Bonding | Chemically fused polyurethane ensures no delamination |
Increased Durability | Withstands heavy loads, impacts, and abrasion |
Resistance to Oils and Chemicals | Suitable for harsh industrial environments |
Lower Rolling Resistance | Enhances forklift efficiency and energy savings |
Shock Absorption & Noise Reduction | Improves operator comfort and safety |
The vulcanization process of polyurethane forklift wheels ensures exceptional performance, durability, and safety. This advanced manufacturing method provides strong adhesion, reducing wheel failures and maintenance costs. As a result, vulcanized polyurethane forklift wheels are the preferred choice for warehouses, factories, logistics centers, and automated systems.