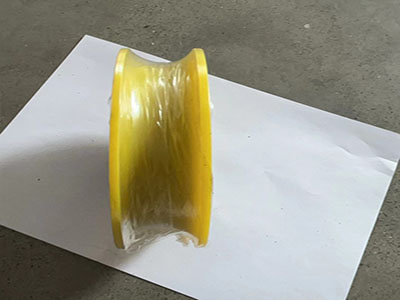
The Electric Stacker Polyurethane Wheel is a key component used in electric stackers (a type of forklift used for lifting and stacking pallets), combining durability, smooth operation, and floor protection. The stacker drive wheel is made of NDI polyurethane elastomer material with higher load capacity, better heat resistance and dynamic performance, which can adapt to high-speed driving and frequent start and stop.According to the actual design of the stacker, the drive wheel is divided into flange holes type drive hub , the spline type drive hub and the flat key drive hub.
Key Features:
1.Material – Polyurethane (PU):
Durability: Polyurethane is resistant to abrasion, cuts, and wear, making it suitable for long-term use in demanding industrial environments.
Load-bearing: PU wheels can support heavy loads without deforming, essential for electric stackers that handle weighty pallets.
Chemical Resistance: Resistant to oils, greases, and many chemicals, which ensures stable performance in various industrial settings.
2.Design:
Typically, these wheels consist of a polyurethane outer layer bonded to a metal core (usually steel or aluminum) to provide both strength and cushioning.
Available in drive wheels, load wheels, and caster wheels, depending on their position and function in the stacker.
3.Performance Advantages:
Low Rolling Resistance: Ensures smooth and quiet operation, reducing energy consumption of the stacker.
Shock Absorption: Helps absorb vibration and impacts, which protects the electric stacker’s components and provides operator comfort.
Non-Marking: PU wheels do not leave marks on warehouse floors, making them ideal for indoor applications.
Quiet Operation: Much quieter than metal or hard plastic wheels, which is beneficial for environments where noise is a concern.
Stacker wheel manufacturing technology
1. Production Preparation: baking materials, color, production preparation.
2. Wheel Injection Molding: Install and clean the mold, input data and start production, and after the wheel is completed, cool it with water, and then clean the burrs.
3. Metal Stamping: Prepare steel raw materials (hot rolled coil), punch molding (top plate, support yoke, large raceway, small raceway), and then weld the shell and support.
4. Surface Treatment: Send the steel shell and accessories to the electroplating factory for galvanizing treatment.
5. Assembly: After galvanized, begin to assemble casters, bearings, bolts and nuts. So a complete castor is complete. Our workers will pack the goods after the final quality inspection.
6. Container Loading: Arrange container loading or transport the goods to the domestic warehouse designated by the customer.
Maintenance Tips:
Regular Inspection: Check for wear, cracks, or embedded debris.
Clean Frequently: Keep the wheels free of grease and debris to maintain traction and extend lifespan.
Proper Load Management: Avoid overloading the stacker to prevent premature wheel failure.
There is no doubt that Philson is the best manufacturer of electric stacker wheels as there is a wealth of expertise and quality products here. Our polyurethane raw materials come from in German Bayer company and Japanese Mitsubishi company with guaranteed quality. With expertise in the industry and a customer-centric approach, Philson ensures that the best and most efficient electric stacker wheels are available to its customers.